R&G Technologie GmbH in Haslach im Kinzigtal is renowned for its outstanding internal grinding expertise. This is demonstrated not only by the large number of customers whoseIncreasingly complex machining tasks and the most demanding requirements are met daily by R&G to the best of their ability, but also 17 high-precision Voumard machines in production.
These superlatives were not expected in 2004. Albert Rißler and Joachim Gärtner, whose initials form the current company name, seized the opportunity 20 years ago and used the spin-off of the grinding shop of a renowned tool holder manufacturer to establish their own contract grinding business. Along with three machines, the two also acquired seven well-trained employees, and their former employer became their client. Today, R&G Technologie GmbH is the largest contract grinding business in southern Germany.
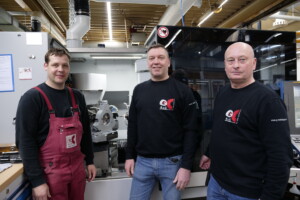
Machine operator Stefan Becherer, production manager Michael Schill and company boss Albert Rißler appreciate the flexibility of the KELLENBERGER VM1000
In addition to grinding, turning and milling were also part of the young company’s portfolio from the very beginning, so that in addition to highly complex workpieces in small and medium series, more and more complete solutions left the company. Today, in addition to tool technology, customers primarily include general mechanical engineering, tool and mold making, medical technology, as well as the automotive industry and its suppliers. Fifty employees now ensure that the high quality so valued by customers is achieved every day. In the internal grinding department, the 17 Voumard machines play their part. The newest, a KELLENBERGER VM1000, was purchased in 2022. It takes the concept of precision to a new level. The traditional Swiss brand Voumard has been part of Kellenberger since 2015.
New machine concept for highest precision
Launched in 2020, the KELLENBERGER VM1000 is the first Voumard machine to be completely redesigned by Kellenberger. It is optimized for flexible, universal internal and external cylindrical machining of complex workpieces up to 300 mm long. The workpiece variety ranges from the smallest individual parts for injection systems in car engines, ball bearing rings and gears, to hydraulic components and complex components in machine tool construction. The strength of the KELLENBERGER VM1000 lies primarily in the area of internal grinding, where it masterfully grinds even the smallest diameters with the highest precision.
The machine concept combines the proven features of Voumard machines, which are still in use in many companies today, with significant innovations. Like KELLENBERGER brand machines, the KELLENBERGER VM1000 features hydrostatic guides on all axes. These highly dynamic linear axes are backlash-free for positioning accuracies in the nano range. Workpieces can be ground with extreme precision with the highest repeatability and machine availability over the entire service life of the machine. Minimal maintenance costs, better machine availability and higher contour accuracy and process reliability are further advantages.
High flexibility thanks to two B-axes and grinding spindle head
The special feature of the KELLENBERGER VM1000 are the two high-precision hydrostatic B-axes: B1 axis with tool holder, B2 axis with workpiece holder. The two B-axes also carry out all necessary movements of the dressing and measuring devices.
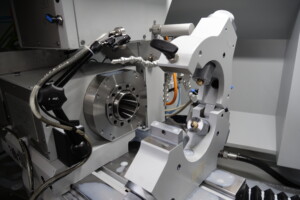
The KELLENBERGER VM1000 was equipped with an SK50 chuck and a quick-clamping device with bar feed.
The tool holder on the B1 axis is equipped with a uniquely compact turret grinding head with flexible grinding spindle arrangement. Spindles and measuring sensors can be optimally positioned and allow the machining of almost any workpiece shape as well as the execution of several internal and external grinding operations in a single setup.
For example, the two B-axes can be swiveled simultaneously by 15° each, for a total of 30°, enabling interpolated taper and center grinding. There’s no question that this requires considerable experience.
The KELLENBERGER VM1000 at R&G has one external grinding spindle and three high-frequency internal grinding spindles with 30,000/45,000 and 60,000 rpm, as well as two measuring devices, one for measuring the workpieces and the other for measuring the grinding wheels, which are then stored in the tool management system. The tool holder on the B2 axis can optionally with a workpiece headstock and a high-precision rotation axis (C-axis) including direct path measuring system and torque motor. This design enables maximum roundness, as well as precision in the fine adjustment of the cylindricity of the inner diameter during cylindrical grinding and brings high precision also for non-circular grinding.
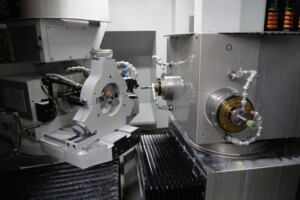
The flexible turret grinding head of the KELLENBERGER VM1000 is equipped with an external grinding spindle and 3 high-frequency internal grinding spindles
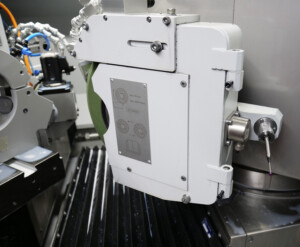
The KELLENBERGER VM1000 is equipped with two measuring probes, one for measuring the grinding wheel (left)
and one for measuring the parts (right)
Company CEO Albert Rißler explains his reasons for purchasing the KELLENBERGER VM1000: “Firstly, the machine’s flexibility, such as its ability to grind non-circular, thread, and jigs, is very beneficial to us. We machine a wide variety of different workpieces every day, often with challenging geometries. One of our specialties is grinding polygon holders. Here, the highest surface and fit accuracy is essential. This cannot be achieved with grinding expertise on the part of the operator alone.”

R&G core competence: grinding of polygon images
Production Manager Michael Schill, who has worked at R&G for 17 years, agrees: “The non-circular grinding of polygonal tool holders is particularly challenging. After machining, two polygonal workpieces must fit together precisely. On the Voumard, this is easily achieved with repeatable accuracy. Even the highest technical requirements are completely unproblematic on the KELLENBERGER VM1000.“
The extensive experience in internal grinding and the unusually high number of individual production runs of highly complex parts ensured that the KELLENBERGER VM1000 was quickly tested down to the smallest detail at R&G. “During non-circular grinding, we noticed something in the software that we only noticed because we were literally splitting the ‘µ’,” says Albert Rißler. “This small anomaly was immediately corrected by Kellenberger IT specialist Jörg Schulz. Here, we saw once again how well and quickly the collaboration with Kellenberger works.”
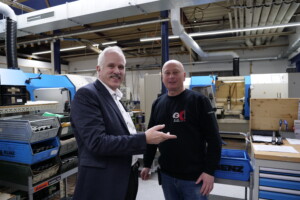
Holger Seitz has been advising Albert Rißler on internal grinding machines for many years
The advice when purchasing the machine is equally excellent. Kellenberger employee Holger Seitz has been familiar with Voumard machines for decades and has been advising R&G in this area for more than 20 years, including on the new KELLENBERGER VM1000: “Many different complex workpieces and special parts, some of which require very difficult machining, present a variety of challenges. Machining polygonal holders is very demanding, the ultimate discipline in grinding, so to speak. Nobody can beat the people at R&G in this area.”
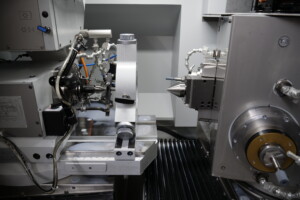
A centering point for the bezel adjustment was one of the special requests from R&G
The requirements for the technological features of the KELLENBERGER VM1000 were correspondingly diverse. Upon request, the machine bed was given an angled milling for better access. Also requested were a centering point for steady rest adjustment and an ISO 50 spindle with SK50 mount, for which a quick-clamping device with a draw-in rod with an accuracy of less than 2 µm was supplied, which had already proven itself on the older Voumard machines. “These requirements were implemented as requested by the specialists in the Customer-Specific Special Design department at Kellenberger,” says Albert Rißler. “With the KELLENBERGER VM1000, we are future-proof in the field of internal grinding.”
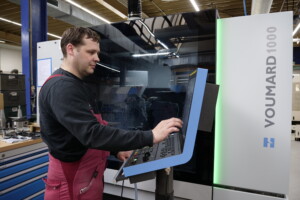
Machine operator Stefan Becherer, a trained grinder and car mechanic, is impressed by the intuitive usability of the BLUE Solution Software