Starting a business always requires a certain amount of risk-taking. “It’s like a motorcycle race. If you don’t want to take any risks, you might miss your chance to win,” says Randy Gevers, the CEO of GRT-Tech with the steely blue eyes and winning smile. He goes without saying that you also need a lot of perseverance, technical acumen, and passion.
Passionate grinder Randy Gevers knows what he’s talking about: Before founding his company GRT-Tech, he enjoyed years of success in motorcycle racing. But his success story doesn’t begin with him, but with his father, Antoon Gevers, who not only instilled in his son a passion for engines and technology, but also for metalworking, and in particular, grinding. Antoon Gevers is something of a grinder whisperer. Like no other, he extracted every last micron from every machine and helped the companies he worked for achieve success in this field over his 50 years of working life. The development of molds for CD presses in 1980 definitively cemented Antoon Gevers’ reputation in the grinding world.
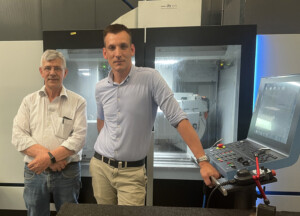
High quality is their trademark: Antoon and Randy Gevers agree:“We both love working in precision engineering at a high level.”
After years of working together as grinders in a company, the Gevers family took the plunge in 2016 – with their father’s early retirement – and went into business for themselves. The first machine Randy Gevers purchased was a conventional grinder, with others following quickly. Fittingly, the first customers came from the KTM world, as the Gevers family had built a large network through racing. Their former employers soon began offering contract manufacturing orders as well.
Today, customers from the aerospace, medical technology, tool and mold making, and packaging industries trust the Gevers, as do the navy, luxury yacht builders, and many more. Among the discerning customers who value GRT-Tech’s work are suppliers to the semiconductor industry. “Theoretically, we could survive on this alone,” says Randy Gevers. “But a company shouldn’t become dependent on one another. And ultimately, it’s the diversity of parts that makes the work so appealing.” The range of materials used at GRT-Tech extends from steel, various stainless steels, brass, and copper to ceramics and plastics. Typically, small batches of up to around 50 pieces are manufactured, but individual parts and prototypes are also produced. Antoon Gevers often manufactures special parts for motorcycles and vintage cars, which customers entrust to him based on his experience.
Randy Gevers quickly realized that machining complex workpieces, such as those used in tool and mold making or medical technology, quickly reached its limits with a conventional grinding machine. So, after moving to the current location in 2018, he purchased a powerful, used Kellenberger KEL-VARIA CNC universal cylindrical grinding machine. “Right from the start, we had a lot of requests for grinding complex workpieces,” says Randy. “But we could only accept around 10% of them. I couldn’t and didn’t want to continue like that.” The decision in favor of a Kellenberger grinding machine wasn’t difficult. Antoon and Randy Gevers knew and valued these machines from their time with their former employer.
The KEL-VARIA is a predecessor model of today’s premium KELLENBERGER K1000 series and, like the KELLENBERGER K1000, stands for the highest machining and surface quality. Its high static and dynamic rigidity and stability are crucial factors for its high precision and high productivity. Hydrostatic guides in all main axes ensure the highest dimensional accuracy for grinding tasks with interpolating axes. The B-axis has a direct drive. This allows the turret grinding head to swivel approximately three times faster and position with an accuracy of less than one arc second. This reduces non-productive time and thus increases productivity, especially when machining requires the swiveling in of different grinding wheels.
Due to the positive experience, another Kellenberger grinding machine quickly found its way to Heeswijk-Dinther, a universal internal and external cylindrical grinding machineKELLENBERGERK100. René van der Peet from the sales company BMT Bridgeport Machine Tools, which has represented the Kellenberger, Hardinge, and Bridgeport brands – all part of the US Hardinge Group – in the Netherlands for years, acted as a consultant. His experience was of great benefit to Randy Gevers in selecting the machine.
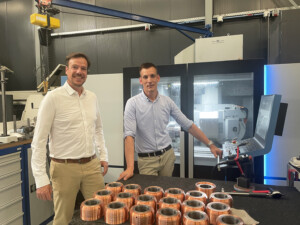
René van der Peet (BMT) configured the KELLENBERGER K100 with Randy Gevers
The KELLENBERGER K100 is available with center distances of 1,000/600 mm and a center height of 200 mm and is designed for workpiece weights up to 150 kg. The high drive power of the grinding wheel ensures increased productivity, while the newly developed Z-guide ensures high profile accuracy. The C-axis with direct drive provides greater precision in non-circular grinding. The machine’s technical highlights include an innovative compact grinding head (10 grinding head variants, 11.5 kW drive power, 500 mm wheel, up to 63 m/s, HF spindles for internal grinding including diagonal and tandem arrangements), a collision-free universal head with three tool and one measuring positions, and a new probe arrangement without a swivel mechanism for increased measuring accuracy.
Randy Gevers chose the longer overall length of 1,000 mm to allow for more flexibility in part size, as well as a grinding head variant with two external grinding spindles, one internal grinding spindle, and a tactile measuring head. The high-frequency spindle, with a speed range of 6,000 to 40,000 rpm, has an internal coolant supply. The machine is equipped with a Fanuc 31i CNC control, and the corresponding software comes from Kellenberger. “I’m fascinated by the machine’s high, reliable accuracy. Added to that are my years of experience, which ultimately makes the difference for the customer,” says Randy Gevers, adding with a laugh: “A machine can’t do the work of advising on how best to manufacture a workpiece.”
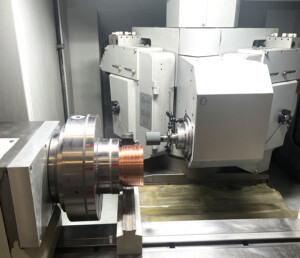
Internal grinding of a workpiece with problematic material combination
Challenging workpieces are part of our daily business, such as the current machining of a component made from a combination of copper and cast iron. The required roughness is < 0.15 µm. “We could also achieve 0.05 µm, but that’s not necessary in this application,” explains Randy Gevers. However: “Cast iron is a very porous, brittle material; the grinding stone clogs up very quickly and must be dressed continuously, but not too often. It’s essentially about finding the right balance. The more experience and sensitivity a grinder has, the more precise such a workpiece will be in the end. Incidentally, this is very expensive due to the material combination and the upstream processes such as turning, milling, and EDM. The grinding process must therefore be perfect right the first time.”
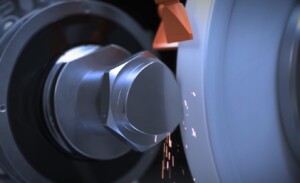
Non-circular grinding of Capto holders
“The more complex the workpiece, the higher the precision requirements, the greater my motivation to perfect it,” says Randy Gevers. He simply loves a challenge. Just not at the racetrack anymore, but with his machines. For the benefit of his customers!

The variety of workpieces for a wide range of industries makes the work exciting